Casting Conversions
Converting weldments and fabrications to castings is an area that can yield great results. Successful conversions offer improved value, lower piece price or improved installed cost by solving other manufacturing problems.
By converting weldments to ductile iron castings, some of the benefits you’ll see are:
- More uniform loading throughout the part
- Improved strength to weight ratio (especially with ADI)
- Reduced internal stress
- Improved machinability, damping characteristics, and appearance
- Elimination of weld zone defects
- Elimination of directional properties
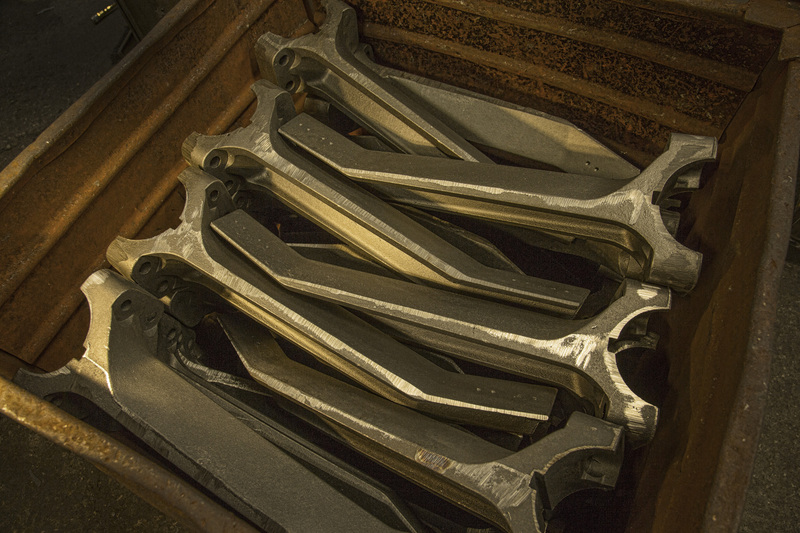
The first thing to look for in a possible conversion to casting is a component with a complex geometry. This could be a single component that was machined or forged, but more often than not the most impressive cost/weight savings is with a series of stampings and/or other wrought shapes that are welded and/or bolted together.
Components often are designed with the building-block mindset during the prototype stages due to design familiarity. However, the “building blocks” usually can be streamlined to one-piece cast components.
The type of complex geometry components that make good conversion candidates to casting often have a high surface-area-to-volume ratio. In addition, they have a high number of inches of weld, which leads to high fabrication costs due to the weld time, material and complicated fixtures. The complex geometry components often also have high aspect ratios, which means that they are long with respect to their width (rangy components). These factors typically indicate where the most cost-savings potential is in a casting conversion.
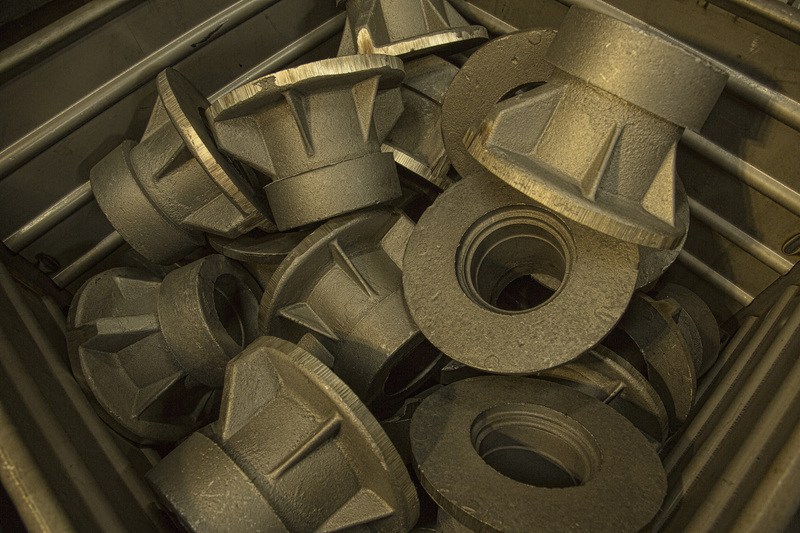