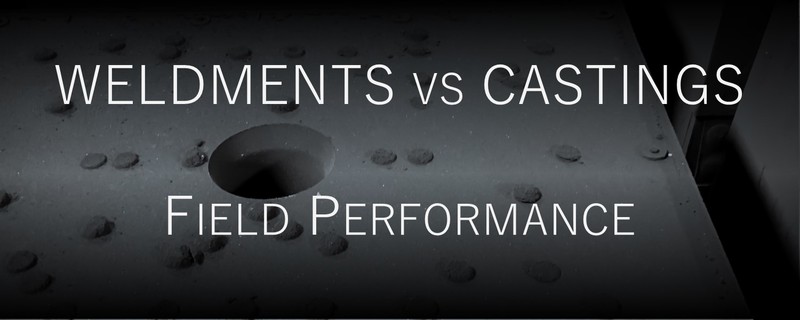
Weldments vs Castings: 3 Reasons To Expect Superior Performance from a Casting
1. CONTROL OVER SHAPE
“The advantage of castings is derived from the ability of liquid metal to assume any shape, shapes that cannot be formed efficiently by any other forming process.” -- John B. Caine
"It is sometimes stated that it is easier to design fabrications from plate and bar because it is easier to visualize a component made as a series of right angled connections. Visualizing a component where there is total freedom of form can be more difficult—it requires the designer to think in three dimensions." -- Malcom Blair and Raymond Monroe, Steel Founders Society of America
Since a casting is not limited like a weldment or assembly by starting out with raw material shapes, we are free to put the material where it is needed in areas of high stress and reduce the material in areas where it is not needed.
This capability offers an incredible amount of control to the creative engineer, whilst simultaneously offering both weight-saving and aesthetic benefits.
As shown in the illustration to the right, from Mr. Caine's 1963 publication, Design of Ferrous Castings, in his words, “the possible decrease in stress by design overshadows the variations in strength of metals to such a degree as to make classic mechanical properties of the metal of minor importance.”
2. ISOTROPIC PROPERTIES vs DIRECTIONAL PROPERTIES
Weldments and Assemblies suffer from anisotropy, which means that a component has strength and ductility in the working direction but has lower transverse properties. In other words, the way the microstructure of the material is oriented will affect the strength and stiffness of the material differently depending on the orientation of the stresses applied, therefore affecting direction of crack formation and propogation.
Cast components do not possess directionality, which engenders confidence in a higher strength, ductility, and toughness than might be associated with a welding or fabricated component. While designers of fabrications must pay strict attention to the directional properties of the materials they're working with and incorporate them into the component’s design (lest the final product become overstressed when a load is applied in the transverse direction), designers of castings have significantly more flexibility.
3. IMPROVED REPEATABILITY, CONFORMANCE, AND QUALITY
When a weldment is converted to a casting it takes out many of the variables inherent to a manual process like welding. Missed welds, inadequate weld size joining material, porosity and pin holes in weld joints, and inconsistency in weld beads or process are all eliminated. Since the casting is produced off of the same production tooling each and every time, the casting process offers incredible consistency. That improved consistency translates directly to the field where failure rates are reduced.
While we often discuss with our customers the cost savings benefits of castings in terms of cost-per-part, it's a valid point to note the reduction of liability derived from producing a more reliable part. The cost of litigation involving a failed weld is the sort of unexpected cost no CFO wants to consider.
It goes without saying we at Smith Foundry are advocates of the casting process, but we do feel there are concrete reasons to move many components that are weldments today to castings. We hope the information we've provided here will be of use when determining the best means of production for your parts.
Nathan C Smith
Director of Business Development
Follow us on LinkedIn to get future updates and other helpful information.